Thermocouples are vital components in a wide range of industrial applications, used primarily for temperature measurement. Understanding their operation, lifespan, and potential failure mechanisms is essential for maintaining accurate temperature control in processes ranging from manufacturing to HVAC systems. In this article, we will explore what causes thermocouples to fail, the signs of malfunction, and how to ensure longevity and reliability in thermocouple performance.
Understanding Thermocouples: A Quick Overview
Before diving into the causes of thermocouple failure, it’s essential to grasp what a thermocouple is and how it works.
What is a Thermocouple?
A thermocouple is a temperature sensor consisting of two different metallic conductors joined at one end. When this junction experiences a change in temperature, it generates a measurable voltage difference due to the Seebeck effect. The voltage produced by the thermocouple is proportional to the temperature difference between the hot junction (where the materials are joined) and the cold junction (reference temperature).
Types of Thermocouples
There are several types of thermocouples, each made from different metal combinations, and their properties influence their suitability for specific applications. Some common types include:
- Type K: Nickel-Chromium vs. Nickel-Alumel, known for its wide temperature range.
- Type J: Iron vs. Constantan, suitable for lower temperatures, but can oxidize quickly.
The choice of thermocouple greatly impacts its reliability and susceptibility to failure.
Common Causes of Thermocouple Failure
Despite their robust design, thermocouples can fail for numerous reasons. Understanding these causes helps prevent premature failure and enhances system performance.
1. Material Degradation
As thermocouples experience temperature fluctuations, their metallic components can undergo wear and degradation.
Oxidation
High temperatures can lead to oxidation of the thermocouple wires, especially in environments rich in oxygen. Oxidation can create an insulating layer on the thermocouple wire, disrupting its electrical conductivity.
Corrosion
Thermocouples used in corrosive environments (like chemical plants) are particularly prone to corrosion. The presence of acids, bases, or other corrosive substances can significantly shorten the lifespan of a thermocouple.
2. Mechanical Stress
Thermocouples are often subjected to mechanical stress from vibrations, shocks, or improper installation.
Thermal Cycling
Repeated thermal cycling can induce fatigue in the thermocouple, leading to cracks or breaks in the wire. This is particularly common in processes where rapid heating and cooling occur.
Improper Installation
Poor mounting techniques can cause bending or twisting of the thermocouple, which may weaken the sensitive junction or lead to further mechanical stress.
3. Environmental Factors
The operating environment plays a critical role in thermocouple performance.
Excessive Temperature
Each thermocouple type has a maximum operating temperature. Exceeding this limit can degrade the materials and cause a complete failure.
Contamination
Contaminants such as dust, moisture, or foreign particles can affect the thermocouple’s contact with the medium it’s measuring, leading to inaccurate readings or failure.
4. Electrical Interference
Thermocouples operate based on very small voltage changes. Therefore, external electrical interference can significantly impact their performance.
Electromagnetic Interference (EMI)
In industrial settings, electromagnetic interference from nearby equipment can introduce noise that disrupts the voltage signal from the thermocouple, leading to erroneous temperature readings.
Ground Loops
Ground loops can also result in inconsistent readings. A proper grounding technique is essential to avoid this issue.
5. Manufacturing Defects
Occasionally, thermocouples may fail due to manufacturing defects.
Poor Quality Control
If the manufacturing process does not adhere to strict quality control standards, defects such as improper alloy composition or poor welding at the junction can occur, leading to premature failure.
Improper Calibration
Inaccurate calibration during installation or maintenance can cause the thermocouple to provide erroneous readings, appearing as a failure when it is merely out of spec.
Signs That Your Thermocouple is Failing
Early detection of thermocouple failure can save money, prevent process inconsistencies, and maintain safety standards. Some common signs of a failing thermocouple include:
1. Erratic Readings
If the temperature readings fluctuate wildly without any changes in the environment, this may indicate that the thermocouple is experiencing electrical interference or internal degradation.
2. Slow Response Time
A thermocouple that takes longer than usual to register temperature changes may have internal damage or insulation breakdown.
3. Reading Out of Range
If the thermocouple reads temperatures significantly outside its expected operating range, it may have suffered from a malfunction.
Preventive Measures to Extend Thermocouple Lifespan
Maintaining temperature sensors is critical for accuracy and efficiency. By taking proactive steps, you can prolong the life and reliability of your thermocouples.
1. Select the Right Type
Choose a thermocouple compatible with your specific application and operating environment. Different metals and junctions are suited to various temperatures and conditions; selecting accordingly can help prevent degradation.
2. Regular Inspections and Testing
Implementing a routine inspection schedule can help catch early signs of wear or damage. Regularly calibrating thermocouples ensures accuracy and helps identify potential failures before they affect the process.
3. Proper Installation Techniques
Ensure that thermocouples are installed according to the manufacturer’s recommendations. Proper mounting, avoiding mechanical stress, and providing adequate support will enhance durability.
4. Minimize Electrical Interference
Use shielded cables for thermocouples, maintain proper grounding, and be cautious of nearby electromagnetic sources to minimize interference.
5. Protect Against Environmental Hazards
Where possible, use protective coverings or sheaths to guard against oxidation, contamination, or corrosion. Consider factors like moisture, acids, and exposure to extreme temperatures during the selection process.
Conclusion
Understanding what causes thermocouples to fail is essential for anyone involved in temperature measurement and control. By prioritizing correct selection, proper installation, and routine maintenance, you can significantly extend the lifespan of these crucial components. Awareness of degradation factors, signs of malfunction, and preventive measures is vital for ensuring that thermocouples continue to function accurately and reliably across various applications.
In conclusion, thermocouples are not invulnerable, and recognizing the causes of their failures is a step toward maintaining operational efficiency and safety in your processes. Investing in quality sensors and systematic monitoring will pay dividends in the long run, safeguarding both equipment and processes in your operations.
What is a thermocouple and how does it work?
A thermocouple is a temperature-sensing device that consists of two dissimilar metal wires joined at one end. When the joined end, known as the measuring or hot junction, experiences a change in temperature, it generates a voltage proportional to that temperature difference. This voltage can be measured and converted into a temperature reading by a thermometer or control system. The other end, called the reference or cold junction, is kept at a known constant temperature to compare against the temperature of the hot junction.
Thermocouples are widely used in various industries due to their durability, wide temperature range, and relatively low cost. There are different types of thermocouples, named based on their metal composition (e.g., Type K, Type J), each suited for specific temperature ranges and applications. However, despite their robustness, thermocouples can degrade over time or due to environmental factors, leading to inaccurate readings or complete failure.
What are common causes of thermocouple failure?
Several factors can lead to the failure of thermocouples. One of the most prevalent causes is oxidation of the metal components due to prolonged exposure to high temperatures or harsh environments. This oxidation can affect the thermoelectric properties of the metals, leading to erroneous temperature readings or complete malfunction. Additionally, mechanical wear and tear, such as vibration or impact, can damage the thermocouple’s structure and function.
Another common cause of thermocouple failure is contamination from the materials surrounding the thermocouple, such as dust, moisture, or corrosive chemicals. These contaminants can compromise the integrity of the junction and alter the thermoelectric output. Furthermore, thermal shock from sudden temperature changes can harm the thermocouple, leading to cracks or breaks in the materials used.
How can environmental factors affect thermocouple performance?
Environmental factors play a significant role in the performance and lifespan of thermocouples. High humidity and moisture can lead to corrosion, especially in environments where the thermocouple is exposed to water or steam. Corrosion can alter the thermoelectric characteristics of the metals used in thermocouples, causing inaccurate readings or failure over time. Additionally, exposure to harsh chemicals, acids, or alkalis can further deteriorate the thermocouple’s materials, leading to a decline in performance.
Extreme temperature changes can also significantly impact thermocouple integrity. Rapid thermal cycling can create stress within the materials, leading to mechanical failure such as cracking or breaking. Even when thermocouples are constructed from high-temperature materials, excessive temperature gradients can lead to thermal fatigue, reducing their effectiveness and potentially leading to a total failure.
Can a thermocouple be repaired, or does it need replacement?
In most cases, thermocouples are not designed to be repaired due to their simple yet sensitive structure. Once a thermocouple shows significant signs of wear, degradation, or failure, it is often more practical and cost-effective to replace it rather than attempt repairs. Replacement ensures accurate temperature readings and the reliability necessary for industrial applications. Regular preventative maintenance, including testing and visual inspections, can help detect issues early, allowing for timely replacements before complete failure occurs.
However, there are situations where inspecting and cleaning a thermocouple can prolong its life and restore its functionality. In cases where contamination is suspected, gentle cleaning with appropriate solvents and materials might improve performance. It is crucial to handle thermocouples with care during such processes to avoid causing further damage to the sensitive junction and metal elements.
How can I extend the lifespan of my thermocouples?
To extend the lifespan of thermocouples, regular maintenance and monitoring are essential. Conducting periodic inspections can help detect signs of wear, contamination, or damage early, allowing for timely intervention. Implementing cleaning protocols to remove build-up or contaminants can also be beneficial, yet care must be taken to prevent physical damage to the thermocouple. Ensuring that thermocouples are installed in appropriate environments, considering factors such as temperature gradients and chemical exposure, will play a significant role in their longevity.
Choosing the correct type of thermocouple for specific applications is another key factor in extending their lifespan. Different thermocouples are built for specific temperature ranges and environments. Selecting a thermocouple that meets the conditions of the application can greatly reduce the risk of failure. Additionally, using protective coverings or thermowells can shield thermocouples from harsh conditions and mechanical damage, further enhancing their durability.
What are the signs of a failing thermocouple?
Identifying a failing thermocouple is crucial for maintaining accurate temperature control systems. One of the most common signs of failure is erratic or fluctuating temperature readings. If the temperature displayed swings unexpectedly or fails to stabilize at an expected value, it could indicate a problem with the thermocouple. Other signs may include slow response times to temperature changes, indicating that the thermocouple is unable to accurately monitor its environment.
Physical inspection of the thermocouple can also reveal signs of degradation. Look for visible damage, such as oxidation, discoloration, or physical wear. If the thermocouple’s wires are frayed or if there is any corrosion present, these are clear indicators of failure. Additionally, persistent readings that are significantly higher or lower than expected can suggest a malfunctioning thermocouple, signaling the need for immediate attention or replacement.
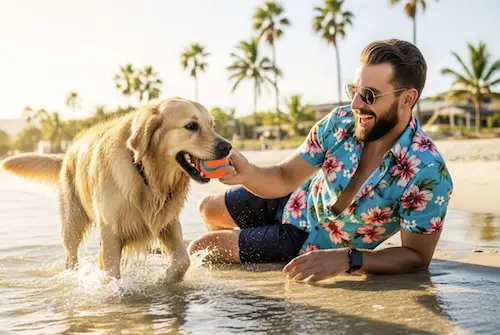
I’m passionate about making home cooking simple, enjoyable, and stress-free. Through years of hands-on experience, I share practical tips, smart meal prep ideas, and trusted kitchen essentials to help you feel more confident in the kitchen every day.