Turpentine is a fascinating and versatile substance, prevalent in various industries such as paint thinner, medicinal products, and natural cleaning agents. Its unique properties make it an essential ingredient in many applications. But how is turpentine manufactured? Understanding the manufacturing process will help us appreciate this valuable natural resource.
What is Turpentine?
Turpentine, often referred to by its chemical name – pine resin distillate, is a fluid obtained from the gum of certain pine trees, primarily the longleaf pine (Pinus palustris). The main active compound in turpentine is terpene, and it is primarily composed of alpha-pinene and beta-pinene. Historically, turpentine has been utilized not only as a solvent but also in the production of synthetic fragrances, varnishes, and even as a fuel source in certain contexts.
The Historical Context of Turpentine Production
Turpentine production dates back centuries and has its roots in ancient practices. The Native Americans were among the first to exploit pine trees for their valuable resin, using it for medicinal purposes and as a waterproofing agent for shelters.
During the 18th century, the production of turpentine became commercialized, particularly in the Southern United States. The rise of the turpentine industry was fueled by increased demand for naval supplies during wartime and the flourishing timber industry.
From Tree to Turpentine: The Manufacturing Process
The manufacturing of turpentine involves intricate stages, from harvesting the raw materials to distillation. Here’s a detailed look at this fascinating process.
1. Harvesting Pine Resin
The first essential step in turpentine production is the harvesting of pine resin. This process involves:
a. Selecting the Right Tree
Not all pine trees can be tapped for resin. The specific species, particularly the longleaf pine, is favored due to its high resin yield.
b. The Tapping Process
To extract the resin, workers make incisions into the bark of the tree. Typically, these incisions are made in a “V” or “U” shape to allow the sap to flow more easily.
Once the sap begins to ooze from these cuts, it is collected in containers fixed to the tree. This method is known as “tapping,” and it is essential to avoid causing significant damage to the tree, allowing it to continue producing resin over time.
2. Collection of Raw Material
After the turpentine sap is collected, it becomes a sticky substance called “oleoresin.” This oleoresin is carefully gathered from the containers and prepared for the next step in the manufacturing process.
3. Distillation Process
The transformation of oleoresin into usable turpentine requires a method known as distillation.
a. Heating the Oleoresin
The oleoresin is heated in a still, which is a container designed to facilitate the separation of liquids through heat. The heat causes the volatile components of the oleoresin to evaporate.
b. Vapor Collection
As the oleoresin is heated, vaporized compounds rise and are captured in a cooler area where they condense back into liquid form. This liquid undergoes a separation process where different compounds are collected based on their boiling points.
The main products obtained from this process are:
- Turpentine: The lighter fraction rich in volatile terpene components.
- Rosin: The heavier, sticky residue that contains the heavier fractions of oleoresin.
4. Purification and Refinement
The crude turpentine obtained from distillation is not yet ready for commercial use. The crude turpentine undergoes further purification to enhance its quality. This is typically done by:
a. Decantation
In this step, the crude turpentine is allowed to settle, enabling impurities to sink to the bottom. The cleaner upper layer is then carefully decanted.
b. Filtration
The turpentine may also be filtered through charcoal or other substances that act to absorb particulates and impurities, resulting in a clearer product.
5. Final Packaging and Distribution
Once the turpentine has been satisfactorily purified, it is packaged in airtight containers to prevent it from evaporating or contaminating. Manufacturers carefully label and store the turpentine for distribution to various industries and shops.
Quality Control in Turpentine Manufacturing
Quality control is an integral part of the turpentine manufacturing process. Various tests are conducted throughout the production to ensure that the final product adheres to industry standards. Some key quality parameters include:
- Purity Levels: Assessing the level of undesirable components.
- Viscosity: Evaluating how well the turpentine flows.
- Odor Characteristics: Ensuring the scent aligns with industry standards.
Regular inspections and adherence to regulations facilitate the production of high-quality turpentine.
Environmental Considerations in Turpentine Production
As with any natural resource extraction, there are environmental implications to consider. However, modern manufacturers are increasingly adopting sustainable practices in the production of turpentine.
Sustainable Harvesting Techniques
Some manufacturers prioritize sustainable tapping methods, ensuring that trees are not overly stressed and can regenerate their sap-producing capabilities.
Reforestation Efforts
Furthermore, many companies engage in reforestation efforts, planting new trees to compensate for those harvested. This helps maintain ecosystem balance and contributes to the overall health of the forests.
Applications of Turpentine
Turpentine’s versatility makes it applicable in a variety of fields. Here are a few prominent uses:
1. Paint Thinner and Solvent
Due to its strong solvent properties, turpentine is often used in paint thinners and varnishes. It effectively dissolves various types of resins and oils.
2. Medicinal Uses
Historically, turpentine was used for its antiseptic properties. It has applications in traditional medicine, although caution must be exercised as it can be toxic in large quantities.
3. Fragrance Production
The fragrant compounds within turpentine also make it a valuable resource in the production of perfumes and aromatic oils.
4. Industrial Uses
Beyond consumer products, turpentine is employed in the manufacture of certain chemicals, plastics, and as a biofuel option in specific processes.
Conclusion
The production of turpentine is a blend of art and science, deeply rooted in a historical context that spans centuries. From the careful harvesting of pine resin to the intricate distillation process, every step contributes to the creation of this versatile substance.
Understanding how turpentine is manufactured not only sheds light on its importance but also highlights the need for sustainable practices to ensure that this natural resource remains available for generations to come. As more industries recognize the value of turpentine, its place in the market may continue to evolve, ensuring that its rich history persists alongside its modern capabilities.
With a renewed appreciation for turpentine, we can celebrate the craftsmanship behind its production and the multitude of applications that benefit from this remarkable fluid.
What is turpentine and how is it used?
Turpentine is a volatile liquid obtained from the distillation of pine resin. It is commonly used as a solvent in paints and varnishes, as well as in the production of certain chemicals and fragrances. Turpentine’s strong solvent properties make it highly effective for thinning oil-based paints and cleaning brushes, rendering it an indispensable tool for artists and craftsmen alike.
Additionally, turpentine has medicinal uses, often found in products aimed at respiratory relief, as well as in traditional folk medicine. Despite its beneficial properties, turpentine must be used with caution due to its strong fumes and potential toxicity, emphasizing the importance of proper handling and ventilation when using it.
What raw materials are used in the production of turpentine?
The primary raw material for turpentine production is pine resin, which is collected from various species of pine trees, especially the Longleaf and Slash pine. The resin is harvested through a process called “tapping,” where incisions are made in the tree bark, allowing the resin to flow out. This tapping method is crucial to ensure a steady supply of resin while minimizing harm to the tree.
In addition to pine resin, other materials may be used in lesser quantities, such as organic solvents for extraction and refinement. The quality and purity of the pine resin significantly influence the final product, making the selection of high-quality raw materials essential for producing superior turpentine.
What are the main steps involved in the manufacturing process of turpentine?
The manufacturing process of turpentine primarily involves harvesting, distillation, and refining. First, raw pine resin is collected from tapped trees. The quality and freshness of the resin play a crucial role in the end product, so quick processing after collection is often essential to preserve its integrity.
After harvesting, the resin undergoes a distillation process where it is heated in a still. During this process, turpentine vaporizes and is collected, while the solid residue, known as rosin, remains. The collected vapor is then condensed back into liquid form, resulting in crude turpentine, which may undergo further refining to remove impurities and enhance its qualities.
How is the distillation process carried out?
Distillation is a critical step in turpentine production. The raw resin is placed in a distillation apparatus, usually a specialized still that allows for controlled heating. As the resin is heated, the lighter components, primarily turpentine, vaporize. This vapor is then directed to a condenser, where it cools and reverts to liquid form.
Careful control of temperature is vital during distillation to ensure optimal yield and quality of turpentine. The temperature needs to be high enough to evaporate the turpentine but low enough to prevent excessive decomposition of the resin. The efficiency of this process greatly impacts the final product’s purity and effectiveness.
What are the environmental impacts of turpentine manufacturing?
The environmental impacts of turpentine manufacturing can vary based on the harvesting methods and processing techniques employed. Sustainable forestry practices are essential to minimize ecological disruption, as excessive tapping may harm pine tree populations and the surrounding ecosystem. Conservation efforts aim to balance industrial needs with environmental preservation by ensuring that only a portion of the resin is harvested without harming the trees.
Additionally, the distillation process can produce emissions if not managed properly. Proper installation of equipment to capture and treat these emissions can significantly reduce the environmental footprint. Manufacturers increasingly strive to adopt environmentally friendly practices to limit the effects on air and water quality associated with turpentine production.
What safety measures should be taken during turpentine production?
Due to its flammable nature and strong fumes, safety measures during turpentine production are crucial. Workers should wear appropriate personal protective equipment (PPE) such as gloves, goggles, and respirators to minimize exposure to turpentine vapors. Adequate ventilation in all work areas is essential to reduce inhalation risks and maintain a safe environment.
Additionally, proper storage and handling protocols are vital to prevent spills and accidents. Turpentine should be stored in designated, labeled containers, away from heat sources and direct sunlight. Regular safety training for personnel involved in the manufacturing process can help ensure compliance with safety regulations and best practices.
How is turpentine refined after distillation?
After the distillation process, the crude turpentine may contain impurities that need to be removed to enhance its quality. This refinement process often involves separating the turpentine from any remaining rosin and other residues, which can be done through further distillation or filtration methods. The aim is to achieve a clear, high-quality product that meets industry standards.
Refined turpentine may undergo additional treatments, such as washing with solvents or neutralizing acids, to improve its odor and purity. The refined product is then analyzed and tested before being packaged for distribution, ensuring it meets the specifications required for various applications, whether in art supplies, industrial uses, or chemical industries.
What are the common uses of turpentine?
Turpentine has a wide range of uses in different industries. One of its primary applications is as a solvent in the paint and varnish industry, where it is valued for its ability to dissolve resins and oils while providing a smooth finish. Artists also frequently use turpentine to thin oil paints and clean brushes, making it a staple in art studios.
Furthermore, turpentine is used in the production of synthetic fragrances, pharmaceuticals, and various industrial chemicals. Its versatility allows it to serve not just as a solvent, but also as a raw material for manufacturing other products, highlighting its significance in both creative and industrial sectors.
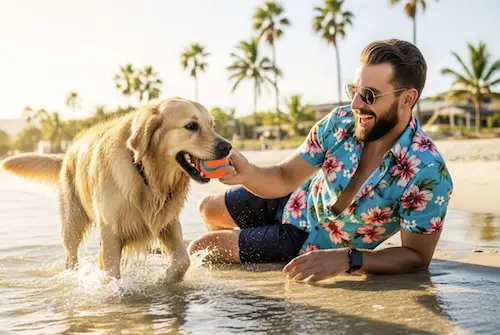
I’m passionate about making home cooking simple, enjoyable, and stress-free. Through years of hands-on experience, I share practical tips, smart meal prep ideas, and trusted kitchen essentials to help you feel more confident in the kitchen every day.