In the vast world of manufacturing, understanding the intricate dynamics of costs is crucial for operational efficiency, pricing strategies, and overall profitability. Two of the most significant components of manufacturing costs are direct labor cost and material cost. While these two terms may be used interchangeably in casual conversations, they represent unique aspects of the production process. This article delves into the fundamental differences between direct labor cost and material cost, their roles in the manufacturing sphere, and their implications for financial management.
Understanding Manufacturing Costs
To grasp the distinction between direct labor cost and material cost, it is essential to first comprehend the broader category known as manufacturing costs. Manufacturing costs encompass all expenditures incurred in the production of goods, which can be divided into three primary components:
- Direct Materials
- Direct Labor
- Manufacturing Overhead
Each of these components contributes to the total cost of manufacturing and plays a vital role in evaluating the financial performance of a manufacturing business.
What is Direct Labor Cost?
Direct labor cost refers to the expenses associated with the wages, salaries, and benefits paid to the workers who are directly involved in the manufacturing of products. This includes assembly line workers, machine operators, and anyone else whose contributions can be directly traced to the production of a specific good.
Characteristics of Direct Labor Cost
There are several characteristics that define direct labor costs:
- Traceability: Direct labor costs can be directly traced to the production of specific products. For instance, if a machine operator spends ten hours assembling a batch of widgets, the labor cost is directly attributed to that batch.
- Variable Nature: Direct labor costs can fluctuate based on production volume. Higher production levels often result in increased labor costs, as more workers may be needed to meet demand.
Components of Direct Labor Cost
Direct labor costs can comprise various components, including:
- Wages: This is the base salary or hourly rate paid to employees directly engaged in manufacturing tasks.
- Employer Payroll Taxes: Employers also incur additional costs such as Social Security and Medicare taxes.
- Benefits: Ongoing benefits (health insurance, retirement contributions, paid time off, etc.) add to the total direct labor cost.
Understanding these components is vital for accurate cost accounting and budgeting.
What is Material Cost?
Material cost encompasses all expenses related to the raw materials and components used in the production of manufactured goods. This could include everything from metal, plastic, and fabric to more specialized materials like chemicals and electronic components. Material costs are a significant part of the total cost of goods sold (COGS) and are essential for calculating the profitability of products.
Characteristics of Material Cost
Material cost has distinct characteristics:
- Intrinsic Value: Material costs are embedded in the physical product itself. The cost reflects the value of materials used in production.
- Output Dependent: The cost of materials also varies based on the volume of production. Larger production runs often lead to discounts from suppliers and a lower per-unit material cost.
Components of Material Cost
Material costs can include several key elements:
- Direct Materials: These are the raw materials essential for the creation of the product.
- Indirect Materials: These materials are necessary for the manufacturing process but do not directly become part of the final product, such as lubricants for machinery.
- Transportation Costs: Expenses related to shipping and handling of raw materials must also be factored in.
- Waste and Scrap: Accounting for waste produced during manufacturing can affect overall material cost calculations.
Comparing Direct Labor Cost and Material Cost
Once we have defined both direct labor cost and material cost, we can now explore the differences between them in more detail.
Definition and Nature
- Direct Labor Cost: This encompasses all expenses related to employee wages and benefits for those directly involved in production. It relates to human resources and their direct contribution to manufacturing.
- Material Cost: This pertains to the expenses for raw materials and components required in the production process. Material costs are product-centric, focusing on the tangible goods involved.
Cost Behavior
- Direct Labor Cost: Generally categorized as a variable cost. Labor costs may increase with higher production levels, but some fixed costs may also apply, such as salaries for supervisory staff.
- Material Cost: Material costs can behave as either fixed or variable, depending on the supply chain and purchasing contracts. For instance, bulk purchases might offer decreased per-unit costs.
Impact on Pricing Strategies
- Direct Labor Cost: Often impacts labor-intensive industries, where labor efficiency directly affects production speed and volume. The more efficient the labor force, the lower the cost per unit, which can enhance competitive pricing.
- Material Cost: Material prices can fluctuate with market conditions, impacting products’ overall cost structure. A sharp increase in material costs can erode profit margins, pushing manufacturers to re-evaluate pricing strategies.
In Accounting Practices
- Direct Labor Cost: Accounting for direct labor involves tracking hours worked and calculating wages and benefits directly linked to production. It is critical for determining labor efficiency and productivity.
- Material Cost: Material costing may involve tracking the purchase, usage, and waste of materials. Various costing methods, such as FIFO (First In, First Out) and LIFO (Last In, First Out), can impact how material costs are recorded and reported in financial statements.
Managing Direct Labor and Material Costs
Understanding the differences between direct labor cost and material cost is vital for effective cost management. Manufacturers need to focus on strategies that help control both elements to maintain profitability and competitiveness.
Strategies for Managing Direct Labor Costs
- Improve Labor Productivity: Training programs and productivity tools can enhance the efficiency of the workforce, ultimately reducing direct labor costs per unit produced.
- Monitor Attendance and Overtime: Keeping a close eye on overtime hours and attendance can help manage labor costs, as excessive overtime can inflate wage expenses.
Strategies for Managing Material Costs
- Negotiate Supplier Contracts: Establishing long-term contracts with suppliers may allow manufacturers to lock in lower prices and prevent unexpected cost spikes.
- Optimize Inventory Management: Close monitoring of inventory levels and adopting just-in-time (JIT) practices can minimize waste and reduce carrying costs associated with raw materials.
Conclusion
In conclusion, the differences between direct labor cost and material cost in manufacturing are not merely semantic; they are foundational to understanding operational efficiency, pricing strategies, and financial management. Direct labor cost pertains to the expenses incurred for the workforce directly engaged in production, while material cost refers to the expenses associated with the raw materials used in creating products.
Both direct labor and material costs are interconnected, influencing the overall cost structure of a manufacturing process. By recognizing and managing these costs effectively, manufacturers can maximize profit margins and enhance their competitive edge in the marketplace. Furthermore, an understanding of these elements allows for more informed decision-making in areas such as budgeting, forecasting, and pricing strategies.
Whether you are a business owner, financial manager, or simply someone interested in the inner workings of manufacturing, appreciating the nuances between direct labor cost and material cost is key to achieving success in the manufacturing industry.
What is direct labor cost in manufacturing?
Direct labor cost refers to the expenses tied directly to the labor involved in manufacturing a product. It includes the wages, salaries, and benefits paid to employees who are directly engaged in the production process. This type of cost can be calculated based on hourly wages or as a salary for employees tasked with specific production roles, such as assembly line workers or machine operators.
Understanding direct labor cost is essential for manufacturers because it directly affects the overall cost of goods sold. By accurately calculating these costs, businesses can better assess their production efficiency and pricing strategies, ultimately leading to improved profitability.
What constitutes material cost in manufacturing?
Material cost, in the context of manufacturing, refers to the expenses associated with the raw materials and components used to produce a finished product. This includes all physical items that are transformed or become part of the final product, such as metals, plastics, fabrics, or other inputs required for production.
Calculating material cost is crucial for manufacturers as it helps them estimate the total cost of production. Accurate assessment of material costs not only influences pricing but also impacts purchasing decisions and inventory management, thus affecting the overall operational efficiency of a manufacturing facility.
How do direct labor cost and material cost differ?
The primary distinction between direct labor cost and material cost lies in their nature and source. Direct labor cost encompasses the human resources involved in the manufacturing process, whereas material cost comprises the tangible elements that are transformed or incorporated into the product. Essentially, direct labor costs are linked to people, while material costs are linked to the substances used in production.
Furthermore, the cost structures associated with these two categories can vary significantly. Direct labor costs are often variable, fluctuating based on the number of hours worked, while material costs can also be fixed or variable, dependent on market prices and availability of raw materials. Understanding these distinctions is vital for effective cost management in manufacturing.
Why is it important to differentiate between direct labor cost and material cost?
Differentiating between direct labor costs and material costs is important for several reasons. First, it allows manufacturers to categorize and analyze costs more effectively, leading to better budgeting and financial forecasting. Accurate costing helps companies determine which areas require improved efficiency, ultimately driving down overall production costs.
Additionally, separating these costs can help in decision-making processes related to pricing strategies. By understanding the components of total production cost, businesses can establish competitive pricing while maintaining profitability. This insight is instrumental in identifying areas for investment and improvement, whether it’s in labor training or optimizing material sourcing.
How do direct labor and material costs contribute to total manufacturing costs?
Both direct labor and material costs play a crucial role in determining the total manufacturing costs. Together, they form the foundation for calculating the overall cost of goods sold (COGS). By combining these two elements, manufacturers can gauge their production expenses accurately, which directly influences their profitability scenarios.
Additionally, understanding the contributions of direct labor and material costs helps management identify cost-saving opportunities. If one component is disproportionately high compared to the other, it may indicate areas where efficiency improvements or cost reductions are needed. This balance is essential for maintaining a healthy profit margin in today’s competitive manufacturing landscape.
Can material costs fluctuate and affect direct labor costs?
Yes, material costs can fluctuate due to various factors such as market demand, supplier pricing, and global economic conditions. These fluctuations can have a cascading effect on direct labor costs, especially when a manufacturer has to adjust production schedules or workforce hours in response to changing material costs. If material prices rise significantly, companies may have to reduce production or implement overtime for employees, thereby impacting direct labor costs as well.
Moreover, when material costs increase, manufacturers may need to reassess their pricing strategies to maintain profit margins. This can lead to changes in workforce planning and direct labor allocation, as businesses look for ways to remain competitive while managing their operational expenses. Thus, monitoring material costs is essential for a holistic financial strategy in manufacturing.
How can manufacturers control direct labor and material costs?
Manufacturers can manage direct labor and material costs effectively through several strategies. For direct labor costs, optimizing workforce schedules, implementing automation, and investing in employee training can significantly improve productivity while minimizing unnecessary labor expenses. Analyzing labor performance metrics can further help identify areas for improvement and efficiency gains.
On the materials front, businesses can negotiate better terms with suppliers, implement just-in-time inventory systems, and continuously assess their sourcing strategies. This proactive approach helps mitigate cost fluctuations and ensures that the manufacturing process remains resource-efficient. Together, these strategies can help manufacturers maintain optimal control over both direct labor and material costs, leading to enhanced profitability.
What are the implications of miscalculating direct labor and material costs?
Miscalculating direct labor and material costs can have serious implications for a manufacturing business. An inaccurate assessment of these costs can lead to improper pricing strategies, which may result in reduced profit margins or losses. When businesses fail to account for the full scope of their expenses, they may find themselves unable to cover operational costs, which could jeopardize their financial stability.
Moreover, miscalculating costs can impact decision-making concerning budgeting and resource allocation. Leaders may Incorrectly anticipate cash flow, which can lead to difficulties in fulfilling orders or maintaining sufficient inventory levels. Hence, it is vital for manufacturers to employ precise accounting practices and continuously refine their cost forecasting to prevent these potential pitfalls.
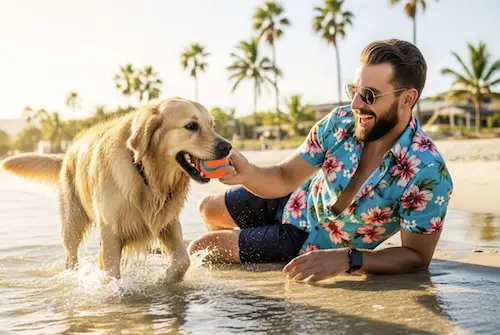
I’m passionate about making home cooking simple, enjoyable, and stress-free. Through years of hands-on experience, I share practical tips, smart meal prep ideas, and trusted kitchen essentials to help you feel more confident in the kitchen every day.