When it comes to metalworking, particularly with challenging materials like cast iron, many novice welders and fabricators find themselves pondering the best methods for cutting through tough materials. One common question that arises is, “Why can’t you cut cast iron with a torch?” This article aims to explore the reasons behind this difficulty, delve into the properties of cast iron, discuss alternative methods of cutting, and offer insights into best practices for working with this robust material.
The Nature of Cast Iron
Cast iron is an iron-carbon alloy containing 2-4% carbon, along with varying amounts of silicon and other elements. This unique composition results in several desirable properties, but it also presents challenges in fabrication.
Properties of Cast Iron
-
Brittleness: One of the fundamental characteristics of cast iron is its brittleness. Unlike ductile metals, cast iron does not deform easily under stress and tends to shatter or crack when subjected to excessive force.
-
High Melting Point: Cast iron has a melting point ranging from approximately 1,200°C (2,192°F) to 1,500°C (2,732°F), depending on its specific type. This high melting point is a significant factor when considering the use of a cutting torch.
-
Thermal Conductivity: Cast iron exhibits relatively poor thermal conductivity compared to other metals such as aluminum or copper. This means that when heat is applied—such as through torch cutting—it can become concentrated in specific areas, leading to thermal stress and cracking.
Types of Cast Iron
To understand why traditional torch cutting is ineffective, it’s essential to recognize the different types of cast iron:
-
Gray Cast Iron: The most common type, widely used in pipes, automotive parts, and machinery. It possesses good machinability but is also quite brittle.
-
Ductile Cast Iron: Often used in applications requiring better ductility and toughness. Despite being more resilient than gray cast iron, it can still pose challenges during torch cutting.
-
White Cast Iron: Known for its hardness due to the presence of cementite. This type is particularly difficult to cut and process.
-
Malleable Cast Iron: Produced by heat treating white cast iron, this form offers improved ductility and is easier to work with than its counterparts.
Each of these types presents unique challenges when it comes to cutting.
The Science Behind Torch Cutting
Torch cutting refers to the process of using a flame, usually fueled by acetylene and oxygen, to melt through metal. While effective for many materials such as steel and aluminum, cast iron does not respond well to this method for several reasons.
Heat Concentration and Thermal Stress
When using a torch, the intense heat generated can create localized melting. However, because of cast iron’s poor thermal conductivity, the heat does not distribute evenly throughout the material. Instead, the surface may appear molten while the interior remains solid. This discrepancy can cause thermal stresses that lead to cracks and fractures in the material, rendering the torch cutting method ineffective.
Inadequate Melting of the Material
Due to its high melting point, cast iron requires a sustained and uniform application of heat to melt adequately. The flames produced by a typical cutting torch are generally not capable of reaching the higher temperatures necessary for cast iron. Even if parts of the iron do melt, the presence of carbon in the iron can lead to the formation of hard, brittle layers, further complicating the cutting process.
Alternative Methods for Cutting Cast Iron
Given the challenges presented by torch cutting, fabricators may need to explore alternative methods to cut cast iron effectively.
Mechanical Cutting Tools
-
Band Saws: A band saw with the appropriate blade can effectively cut through cast iron. When selecting a blade, it is crucial to choose one designed for metal cutting, as these are typically made from high-speed steel or carbide materials.
-
Angle Grinders: Equipped with a metal cutting disc, angle grinders can effectively cut cast iron. They are versatile and can be used for various cutting tasks.
-
CNC Machines: Computer Numerical Control (CNC) machines with appropriately configured cutting tools can produce precise cuts in cast iron. This method is ideal for intricate designs or large-scale production.
Grinding Techniques
In some cases, grinding can be an effective way to shape or reduce the thickness of cast iron. Tools such as bench grinders or hand-held grinders allow for precise control and are less likely to cause the type of thermal shock associated with torch cutting. Here are some important aspects of grinding cast iron:
-
Use of Coolants: Applying coolants during the grinding process can help mitigate heat buildup, preserving the integrity of the material.
-
Choosing the Right Abrasive: Selecting the appropriate grinding wheel is crucial. Using wheels designed for ferrous metals will yield better results.
Best Practices for Working with Cast Iron
To ensure successful cutting and fabrication of cast iron, certain best practices should be followed:
-
Pre-heat the Material: If using a torch for any reason, pre-heating the area to raise the temperature slightly can help in mitigating the effects of thermal shock. However, caution is advised, particularly with torch applications.
-
Maintain Sharp Tools: Keeping cutting tools sharp ensures clean cuts, minimizing additional pressure and stress on the material.
-
Cut Slowly and Steadily: Whether using a saw, grinder, or CNC machine, cutting at a moderate pace allows for fidelity of cuts and reduces the risk of fracturing.
-
Safety Precautions: Always wear appropriate personal protective equipment (PPE). When working with cast iron, molten metal may pose risks that need to be addressed through proper safety gear.
Conclusion
In summary, while torch cutting may be a viable method for many metals, it falls short when it comes to cast iron due to its brittleness, high melting point, and poor thermal conductivity. Understanding the material’s properties is crucial for anyone looking to work with cast iron.
By employing alternative cutting methods such as mechanical cutters or grinding techniques, and adhering to best practices, fabricators can achieve success in their projects involving cast iron. The complexity of cutting this robust material should not deter you; rather, it should encourage you to seek out innovative solutions tailored to its unique properties. Only through understanding and proper technique can one successfully navigate the challenges posed by cast iron cutting, leading to effective results and durable constructions.
Why can’t I cut cast iron with a torch?
Casting iron has a high carbon content, which gives it strength and durability, but also makes it challenging to cut with a torch. When exposed to the intense heat of a torch flame, the cast iron can melt unevenly, leading to structural weaknesses. Additionally, the melting point of cast iron is significantly higher than that of many other metals, making it difficult to achieve a clean cut.
Trying to cut cast iron with a torch can also produce slag, which is the molten waste material created during cutting. This slag can become fused to the iron, making it hard to achieve a precise cut. Furthermore, if the cast iron has pre-existing flaws or cracks, the intense heat can exacerbate these issues, potentially causing the piece to break apart rather than yield a clean cut.
What are the best tools to cut cast iron?
For cutting cast iron, tools such as a band saw, abrasive saw, or a cold saw are much more effective than a torch. These machines are designed to handle the hardness and brittleness of cast iron, allowing for cleaner and more controlled cuts. A band saw, for example, can cut through cast iron with precision and reduce the risk of heat-induced cracks.
Another option is using a diamond-tipped saw blade, which is ideal for cutting through hard materials like cast iron. This tool helps maintain a cooler cutting temperature, which reduces thermal stress on the material. Regardless of the tool chosen, using lubrication and maintaining a proper cutting speed will also enhance the cutting efficiency and longevity of both the tool and the cast iron piece.
Does the thickness of the cast iron affect cutting methods?
Yes, the thickness of the cast iron significantly impacts the cutting method used. Thicker pieces of cast iron require more robust cutting tools and often a more powerful method, such as a band saw or industrial cutting torch designed specifically for heavy-duty applications. Thicker materials also tend to have more residual stress and can crack if not handled properly.
For thinner cast iron pieces, more versatile cutting methods like using a reciprocating saw or even manual cutting tools, such as hacksaws, can work effectively. No matter the thickness, it is crucial to assess the material and choose a cutting method accordingly to ensure a successful and safe outcome.
Is it safe to cut cast iron with a torch?
Cutting cast iron with a torch is generally not considered safe. The process can create a significant amount of heat, leading to the risk of the material cracking or splintering, which can result in flying debris and personal injury. Additionally, the toxins produced from burning oil or other materials associated with cast iron could pose health hazards without proper ventilation and safety equipment.
Moreover, the unpredictable melting of cast iron with a torch can lead to burns and other injuries if not done with caution. Areas nearby could also be at risk of catching fire from the sparks produced during the cutting process. For these reasons, it is recommended to use methods that offer greater control and safety when working with cast iron.
What happens to cast iron when heated too much?
When cast iron is heated excessively, several undesirable phenomena can occur. The first is that it may begin to melt or warp, leading to structural failure. This is particularly problematic if you are attempting to join or cut cast iron, as the excess heat can create areas of weakness in what should be a solid piece of metal. The risk of cracking increases dramatically when cast iron is subjected to high temperatures without proper cooling methods.
Additionally, overheating cast iron can alter its chemical structure, potentially leading to a phenomenon known as “graphitization,” where the carbon in the iron starts to break down. This change can compromise the material’s integrity and reduce its overall performance in applications where strength and durability are critical. Therefore, it’s crucial to control the heat applied to cast iron, especially when cutting or welding.
Can I use a plasma cutter on cast iron?
Using a plasma cutter on cast iron is possible, but it should be approached with caution. Plasma cutters can produce very high temperatures, allowing them to cut through a variety of metals, including cast iron. However, just like with torches, the high heat can lead to the formation of slag and weaken the material structure, particularly if not done correctly.
Before using a plasma cutter on cast iron, it’s essential to consider the thickness and potential heat damage. Employing the right settings, including air pressure and cutting speed, can minimize the risks associated with heat distortion. Appropriate protective measures should also be taken to safeguard against flying debris and hot metal splatter during the cutting process.
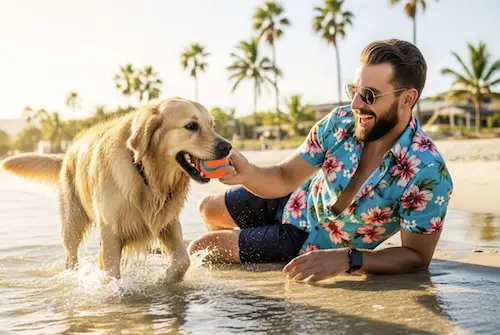
I’m passionate about making home cooking simple, enjoyable, and stress-free. Through years of hands-on experience, I share practical tips, smart meal prep ideas, and trusted kitchen essentials to help you feel more confident in the kitchen every day.